From my field experience, Why I see BIM is one of the most important tools for facilities management.
As a facility maintenance engineer with experience managing construction upgrades, I’ve seen personally how crucial every detail is in handling a project. Effective data collection from stakeholders and clear communication are the cornerstones of project success. However, I’ve also witnessed that traditional methods like paper-based plans and scattered verbal information can lead to misunderstandings and costly mistakes. For maintenance, the lack of centralized information makes it difficult to track maintenance schedules, identify potential problems early on, and perform preventive maintenance efficiently.
So the more precise and organized the data, the smoother the project runs. My studying and experience in project management and strategic thinking have always helped me anticipate problems and ensure project requirements align with stakeholder goals.
Then, I discovered Building Information Modeling (BIM). Since I started learning BIM software like Revit it has opened my eyes to a new world of possibilities. It became clear how BIM could revolutionize project management by streamlining processes and eliminating costly mistakes caused by data gaps and miscommunication. In essence, BIM acts as a central data hub, empowering project managers to achieve peak efficiency. I’m also interested in exploring how BIM can be used for energy management within facilities.
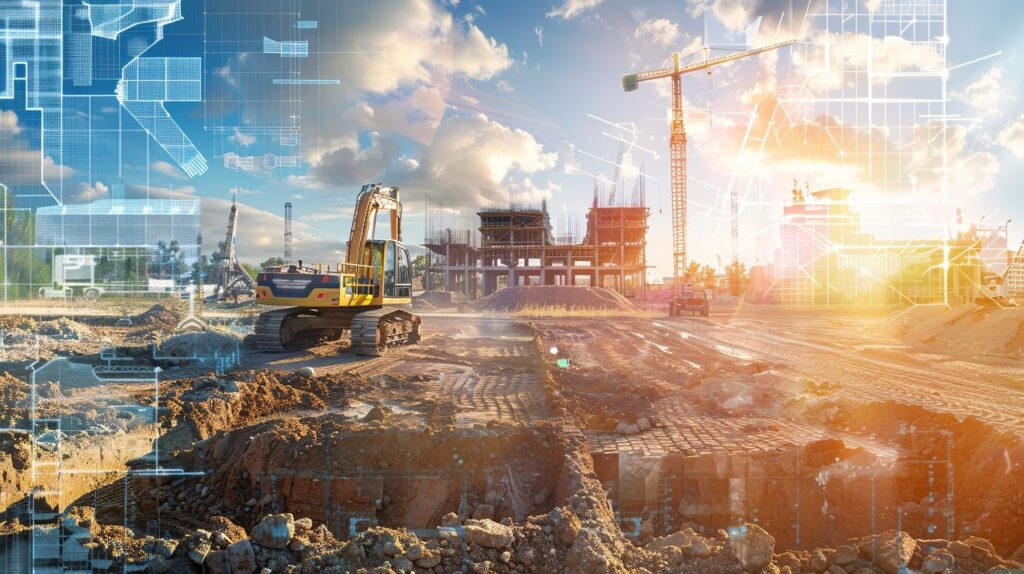
So, What is BIM?
BIM can be broken down into two main parts: Building Information Modeling.
Building refers to the fact that BIM creates a digital representation of a building project, like a 3D model. But unlike a simple drawing, this model is much richer.
Information Modeling is where things get really interesting. Imagine each element in the model, like a wall or window, isn’t just a visual element. It holds information like:
- Material type (brick, concrete, etc.)
- Cost of materials.
- Manufacturer Details.
- Maintenance requirements.
Those data are all connected to the model, so if you change a window style, the software can automatically update the cost and material information. Pretty helpful, right?
BIM is more than just 3D modeling software. It’s a collaborative process for creating and managing information-rich digital representations of a building project. This data-driven approach integrates all aspects of a building – architectural design, structural elements, building systems (electrical, plumbing, HVAC) – into a single, intelligent model.
BIM: A Recipe for Project Management Success
BIM offers a multitude of benefits that streamline project management, from design to completion:
- Enhanced Collaboration: BIM acts as a central hub for real-time information sharing. All project stakeholders – architects, engineers, contractors, and facility managers – can access and update the model simultaneously, fostering better communication and reducing the risk of misunderstandings.
- Clash Detection and Resolution: Imagine identifying clashes between piping and electrical conduits before they snarl up construction! BIM software can proactively detect these conflicts within the digital model, allowing teams to address them virtually, saving time and money on costly rework later.
- Improved Efficiency and Cost Savings: With BIM, accurate quantity take-offs can be generated directly from the model, leading to more precise material ordering and reduced waste. Additionally, BIM facilitates the prefabrication of building components off-site, minimizing on-site construction time and labor costs.
- Simulations for Better Decision-Making: BIM allows for virtual walkthroughs and simulations of the construction process, enabling teams to identify potential logistical challenges and optimize workflows. This foresight empowers better decision-making throughout the project lifecycle.
The Downside of Not Using BIM
While BIM adoption is on the rise, some projects continue to rely on traditional, less efficient methods. This can lead to:
- Communication issues: Without a central platform, information sharing can be fragmented, increasing the risk of errors and miscommunication.
- Clash Detection During Construction: Identifying clashes on-site can halt construction, leading to delays and cost overruns.
- Reduced Efficiency: Traditional methods often involve manual processes and data re-entry, hindering overall project efficiency.
BIM: Building a Future of Efficiency
Personally, I’m very convinced that BIM isn’t just a trend; it’s the future of project management. By embracing this technology, construction professionals can build a better tomorrow that’s collaborative, efficient and delivers exceptional results.