Why Maintenance Engineering Matters (and How We Do It)
Being a maintenance engineer means that you will not get the spotlight as often as in some other roles. but let me tell you, keeping the machine running – literally and figuratively – is a crucial part of any operation. Maintenance engineering is all about ensuring equipment, infrastructure, and processes function at their best. It’s the invisible hand that keeps things working, preventing costly breakdowns and ensuring safety.
The satisfaction of keeping things running smoothly is what makes maintenance engineering such a rewarding career. While troubleshooting breakdowns is part of the job, the greater reward comes from preventing them in the first place.
So how do we achieve this?
Well, we have a toolbox full of methods, each suited for different situations. Here’s a peek inside:
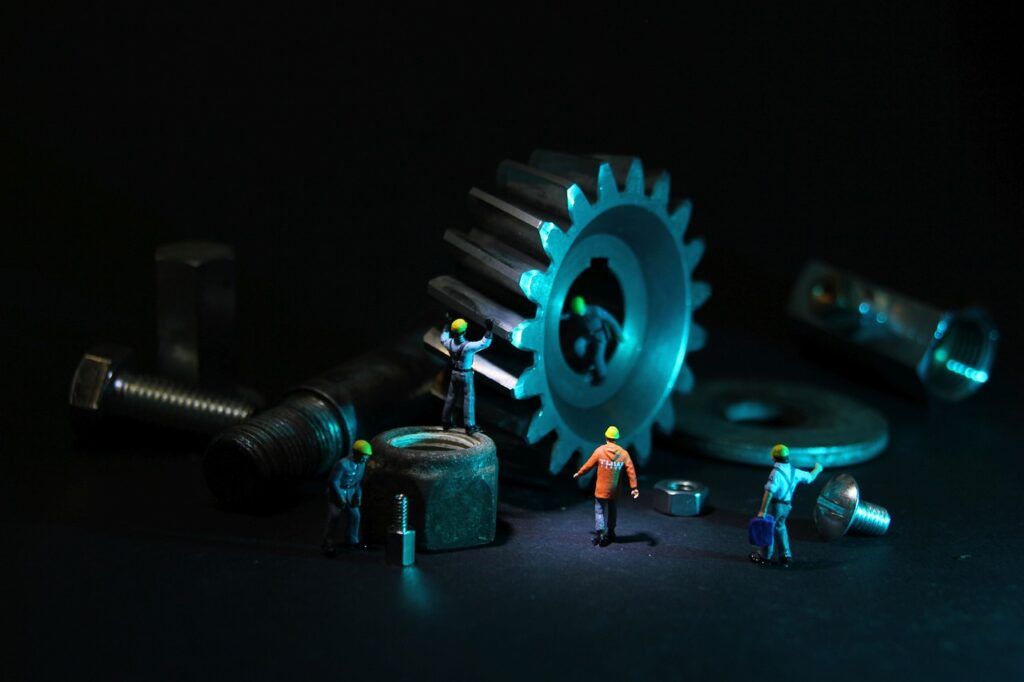
Maintenance methods.
1- Preventive Maintenance:
This is our proactive approach. Think of it as regular checkups for your car. We follow schedules to inspect equipment, identify minor issues, and perform routine maintenance tasks like lubrication and adjustments. This catches problems early, preventing them from snowballing into bigger, more expensive repairs.
- scenario: Let’s say we’re a maintenance team for a large factory.
- Equipment: The rooftop HVAC (heating, ventilation, and air conditioning) unit.
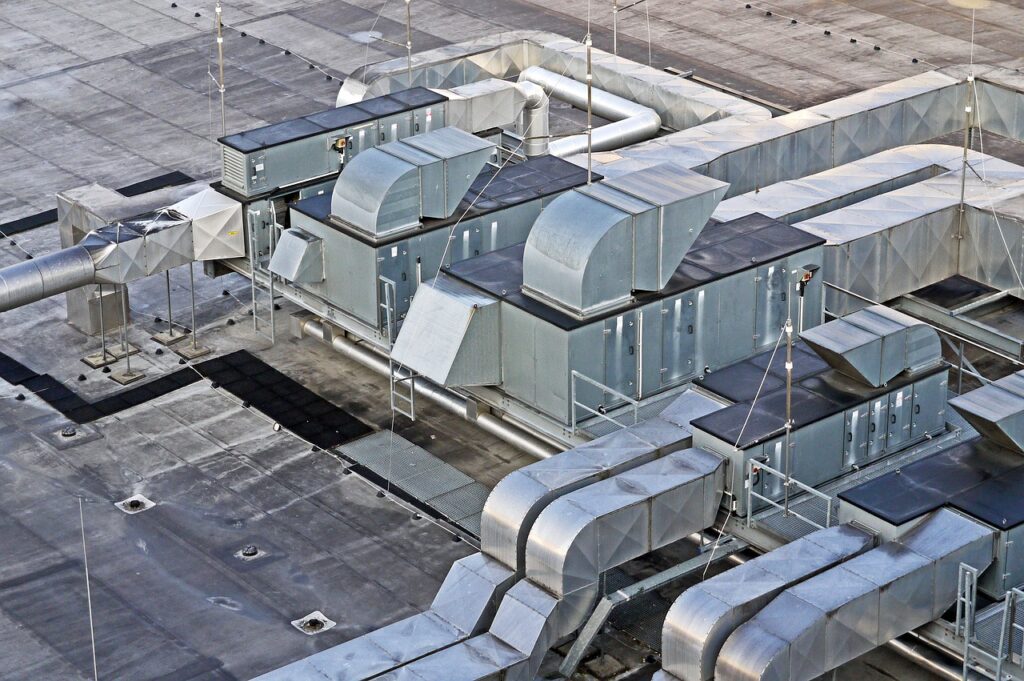
- Preventive Maintenance Tasks would be something like:
- Schedule: We follow a bi-annual (twice-a-year) inspection schedule for the HVAC unit.
- Inspection: During the inspection, we’ll:
- Check air filters and replace them if clogged. Dirty filters restrict airflow, reducing efficiency and potentially causing the unit to overheat.
- Inspect belts and pulleys for wear and tear. Worn belts can slip, reducing efficiency and putting strain on the motor.
- Clean condenser coils to remove dust and debris. Clogged coils reduce heat transfer, forcing the unit to work harder and use more energy.
- Top up refrigerant levels if needed. Low refrigerant reduces cooling capacity.
- Lubricate moving parts to minimize friction and wear.
2-Predictive Maintenance:
Here, we get a little more sophisticated. We use things like vibration analysis and oil testing to monitor equipment health and predict potential failures. This allows us to schedule maintenance before a breakdown occurs, minimizing downtime and maximizing efficiency.
- Imagine a scenario: it’s a scorching summer afternoon, and the demand for electricity is at its peak. Homes and businesses are cranking up their air conditioners, putting a huge strain on the power grid. Suddenly, a critical turbine at a power plant fails. The entire plant goes offline, plunging thousands into darkness. This is exactly why predictive maintenance is so crucial in the power generation industry. Here’s how it helps prevent such catastrophic events:
- The Equipment: A massive gas turbine, the heart of the power plant, spins at high speeds to generate electricity. Even the slightest imbalance or misalignment can cause excessive wear and tear.
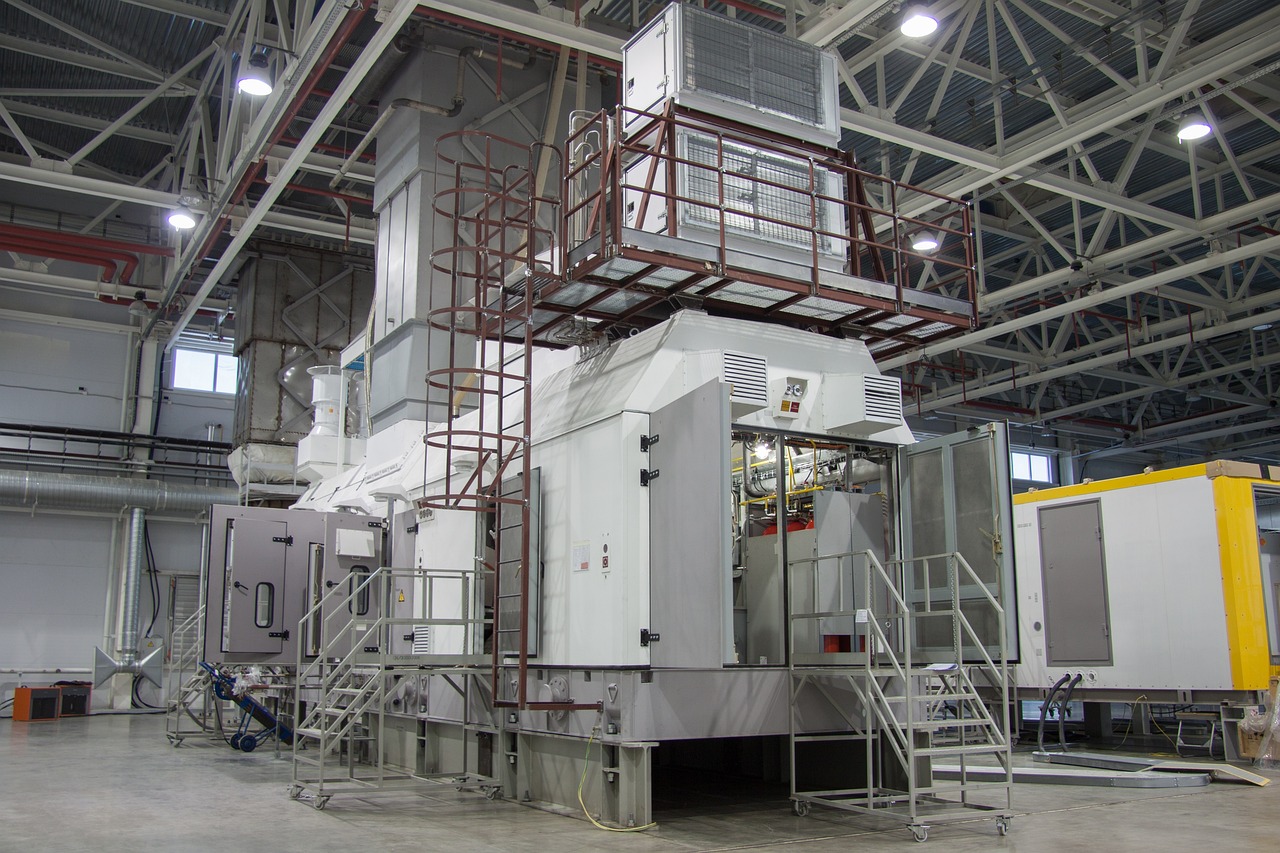
- Predictive Techniques:
- Vibration Analysis: Sensors are placed on the turbine housing to continuously monitor vibrations. These vibrations can reveal problems like imbalances, bearing wear, or shaft misalignment.
- Oil Analysis: Oil samples are regularly extracted from the turbine and analyzed for the presence of wear particles and changes in viscosity. This can indicate internal problems within the turbine.
- Early Warning Signs: If the data from the sensors and oil analysis shows any abnormal trends, such as increasing vibration levels or the presence of metal particles in the oil, it’s a red flag. This could signal a potential failure in the making.
- Taking Action:
- Early Intervention: With this early warning from predictive maintenance, engineers can schedule maintenance before a catastrophic breakdown occurs. This might involve:
- Detailed Inspection: Using specialized tools, technicians can perform an internal inspection of the turbine to diagnose the exact issue.
- Repair or Replacement: Based on the inspection findings, worn components can be repaired or replaced to prevent a complete failure.
- Benefits of Predictive Maintenance:
- Prevents Power Outages: By catching potential turbine failures early, predictive maintenance helps ensure a reliable and continuous supply of electricity, preventing widespread blackouts.
- Maximizes Efficiency: Regular maintenance keeps the turbine operating at peak performance, maximizing its efficiency and minimizing fuel consumption.
- Reduces Costs: Predictive maintenance helps avoid the high costs associated with unexpected equipment failures, such as emergency repairs and potential damage to other plant components.
In the high-pressure environment of power generation, where even a brief power outage can have significant consequences, predictive maintenance is an invaluable tool. It allows engineers to take a proactive approach, ensuring a reliable and efficient power supply for homes and businesses.
3- Corrective Maintenance:
Let’s be honest, breakdowns happen. When they do, corrective maintenance comes into play. This is where we diagnose the problem, repair or replace faulty components, and get things back up and running as quickly as possible.
- Scenario: Imagine you’re a maintenance engineer in a busy factory. The production line is humming along, churning out widgets at an impressive pace. Suddenly, the frantic shouts of a line worker pierce the air. The conveyor belt that carries parts throughout the assembly line has stopped – a complete halt in production. This is a classic scenario for corrective maintenance. Here’s how it unfolds:
- The Problem: The conveyor belt has malfunctioned. It’s not moving, and the production line is at a standstill.
- Diagnosis: Your first task is to identify the cause of the failure. You’ll:
- Visually Inspect: Walk the length of the conveyor looking for any obvious signs of trouble, such as a broken belt, jammed rollers, or a malfunctioning motor.
- Check Controls: Ensure the control panel is functioning correctly and that there are no tripped breakers or electrical issues.
- Taking Action:
- Repair or Replace:
Once you’ve diagnosed the problem, it’s time to fix it. This might involve:- Replacing a broken belt section.
- Unjamming a seized roller and relubricating it.
- Resetting a tripped breaker or fixing a minor electrical fault.
- Testing and Adjustments: After repairs are complete, you’ll test the conveyor belt to ensure it’s functioning properly. This might involve running it unloaded at first, then gradually increasing the load to normal operating conditions.
- Getting Back Online: The key in corrective maintenance is speed. The faster you diagnose and fix the problem, the sooner the production line can get back up and running. Every minute of downtime translates to lost productivity and potential revenue.
- The Importance of Corrective Maintenance:
While corrective maintenance is reactive to breakdowns, it plays a vital role in any operation. By effectively troubleshooting and repairing problems, you can:- Minimize Downtime: The quicker you fix a breakdown, the less time production is halted.
- Prevent Further Damage: Prompt repairs can prevent minor issues from escalating into more serious problems.
- Maintain Equipment Lifespan: By addressing problems as they arise, you can help extend the lifespan of your equipment.
Even though corrective maintenance deals with fixing what’s broken, it’s still an essential part of keeping things running smoothly in any production environment.
4- Condition-Based Maintenance CBM:
This blends aspects of preventive and predictive maintenance. We continuously monitor equipment performance using sensors and data analysis. This allows us to tailor maintenance schedules based on the actual condition of the equipment, optimizing resource allocation and preventing unnecessary maintenance.
- Scenario: Imagine you’re a maintenance engineer for a wind farm. These massive turbines operate 24/7, generating clean energy. However unexpected breakdowns can be costly, requiring specialized technicians and potentially halting energy production. This is where condition-based maintenance (CBM) comes in. Here’s how it helps keep the turbines spinning:
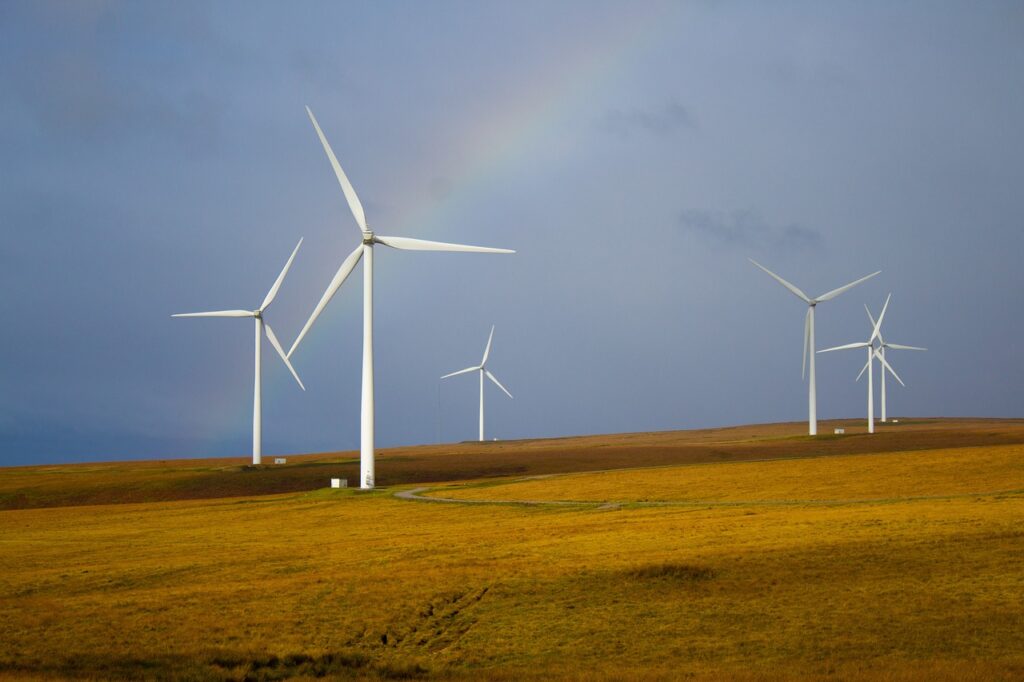
- Sensors and Data: Each wind turbine is equipped with a network of sensors that continuously monitor various parameters, such as vibration levels, gearbox oil temperature, and wind speed. This data is transmitted wirelessly to a central monitoring system.
- Real-Time Analysis: Software analyzes the incoming data streams in real-time, looking for trends or anomalies. For example, a gradual increase in gearbox temperature might indicate potential bearing wear.
- Predictive Insights: Based on the data analysis, the system can predict when a component might be nearing failure. This allows for proactive maintenance scheduling.
- Tailored Maintenance: Instead of following a rigid schedule, maintenance is performed based on the actual condition of the equipment. If a sensor reading indicates a potential issue, technicians can be dispatched to inspect the turbine and address the problem before it leads to a breakdown.
- Benefits of CBM:
- Optimizes Maintenance: CBM prevents unnecessary maintenance on healthy equipment, freeing up resources for critical tasks.
- Prevents Breakdowns: Proactive maintenance based on real-time data helps avoid unexpected failures and costly downtime.
- Extends Equipment Life: By catching problems early, CBM helps prevent minor issues from escalating into major repairs, extending the lifespan of the wind turbines.
In the ever-changing environment of a wind farm, CBM provides a dynamic approach to maintenance, ensuring the turbines operate efficiently and reliably. While the initial investment in sensors and data analysis systems can be significant, the long-term benefits of avoiding costly breakdowns and extending equipment life often outweigh the upfront costs.
Don’t Forget: Maintenance is Done by a Team
Now, none of these methods are effective without the right people behind them. This is where a well-qualified engineering team comes in. We need engineers who understand the intricacies of the equipment, can analyze data effectively, and make sound decisions. But it’s not just about qualifications – a well-trained team of technicians is crucial too. Regular training ensures everyone is up-to-date on the latest tools and technologies, fostering a culture of continuous improvement.
In my experience, a highly skilled and well-coordinated maintenance team is the hidden engine that drives any successful operation. By strategically applying the right methods and investing in our people’s development, we ensure things run smoothly, safely, and efficiently. That’s what motivates me to come to work every day – knowing I play a crucial role in the bigger picture and contribute to keeping everything running like clockwork.
I have recently started a blog, the information you offer on this website has helped me greatly. Thanks for all of your time & work.
Greetings! Very helpful advice on this article! It is the little changes that make the biggest changes. Thanks a lot for sharing!